The True Cost of Your Business Risks
- July 25, 2024
- Best Practices
- Automation
How manufacturers can quantify the financial impact of their business continuity risks
You might know about the risks your business faces, but do you know the financial impact of those risks? Every action (or inaction) you take adds or reduces risk for your business and affects your bottom line. How do you quantify risks that could interrupt your business operations and use that information to inform the decisions you make? Follow these steps to quantify and reduce your business continuity risks.
STEP 1
SET GOALS & ASK QUESTIONS
You’re never going to eliminate risk, but to lower your risks, you need to understand your goals and spend time with people in different areas of the business. What are your customers asking of you? What will you need to do to meet their needs? What could go wrong, and how will you respond? Once you’ve identified areas that could interrupt your business, you can quantify the potential financial impact of those situations.
STEP 2
IDENTIFY YOUR CYBERSECURITY VULNERABILITIES
What kinds of challenges could have negative financial effects on your business? Cybersecurity incidents can be particularly costly in several ways. In a 2023 report, the global average cost of a data breach was $4.45 million and $4.73 million in the industrial sector.[1] What makes cybersecurity risks so costly?
- Ransomware is one of the most common forms of cybercrime. Last year, the average ransom paid by manufacturers was $361,000.[2]
- You’ll have to figure out how the data breach occurred to prevent it from happening again. Manufacturers paid an average of $48,486 in forensic investigation costs to discover the root cause, and 36% never even find the root cause. [2]
- The average organization takes 277 days to identify and contain a data breach. [1] How much production do you risk losing in that time frame?
- Can you put a price on reputation? Publicly traded companies are required to report a data breach that affects their customers, which puts them at risk of losing customers and even legal repercussions.
- If you can’t recover control of your equipment, you face the cost of replacing and re-installing your entire network infrastructure.
The good news is there are ways to reduce your financial cybersecurity risks. Organizations that extensively use security AI and automation identify and contain data breaches an average of 108 days faster than organizations that don’t use them. [1]
STEP 3
LOCATE YOUR SKILLS GAPS AND WORKFORCE CHALLENGES
Cybersecurity incidents can be even more costly if you have skills gaps in your workforce. The average cost of a breach for organizations with high levels of security skills shortage is $5.36 million.[1] Skills gaps are costly in other ways too. By 2030, U.S. manufacturing is expected to have 2.1 million unfilled jobs.[3] If you can’t replace that skilled workforce, you are vulnerable to risks like unplanned downtime, loss of production and poor quality. Do you know how costly it can be if you don’t have the right workforce strategy?
The most effective workforce strategies are based around training, supporting and augmenting workers with the knowledge, resources and technology they need to be successful. The cost of replacing an individual employee can range from one-half to two times the employee’s salary.[4] Giving your workforce the knowledge, tools and resources it needs to perform at a high level can lead to an increase in job applicants, lower turnover and record growth.
STEP 4
CALCULATE YOUR COST OF POOR QUALITY
In Rockwell Automation’s 9th annual State of Smart Manufacturing Report, manufacturers said quality was their number one focus for smart manufacturing. When you consider the financial impact of poor quality, it’s easy to see why. Poor quality can be costly in several ways:
- The average cost of a food recall is around $10 million in direct costs.[5]
- The average insurance claim for manufacturing product recalls is roughly $780,000.[6]
- If your product is recalled, how much will it cost to fix and replace the product without being able to profit from that production?
- Your reputation is again on the line. If your quality issue harms the end user, it can cause public health and safety concerns and damage your reputation.
Implementing a digital quality management system (QMS) can reduce your cost of poor quality by lowering the risk of human error and easing the burden on your operators. In a case study on the economic impact of the Plex smart manufacturing platform, one organization reduced its annual inventory waste by $800,000.[7] When you understand your cost of poor quality and gain more insight into your data, you can make more informed decisions to improve quality and lessen the financial impact of your quality risks.
STEP 5
ASSESS YOUR MAINTENANCE STRATEGY
Do you have a predictive maintenance strategy? If not, you risk unplanned downtime, unnecessary labor and shorter equipment lifespan. Using a computerized maintenance management system like Fiix can make a difference in your bottom line.
For example, Fiix users have 10% reduction in production-related costs and operating expenses, 20% reduction for mean-time-to-repair, 27% reduction in asset-related unplanned downtime incidents and are 73% more efficient in equipment inspections.[8] When you add together the reduction of operating costs, uptime and labor savings, you can quantify the financial impact of reducing your maintenance risks.
STEP 6
HAVE A BACKUP PLAN
Once you quantify which areas of your business present the biggest risks, you can prioritize which areas to address first. It is important to note that even if you modify your operations to address risks, you can only control so much. There’s no way to completely eliminate risk, so you need to have the right insurance in place to protect your business.
FINAL STEP
WORK WITH AN EXPERT
While many of these numbers and statistics are based on national averages, small to medium sized manufacturers can differ drastically from large corporations. To get a more personalized assessment of your financial risks, work with Van Meter’s smart manufacturing team.
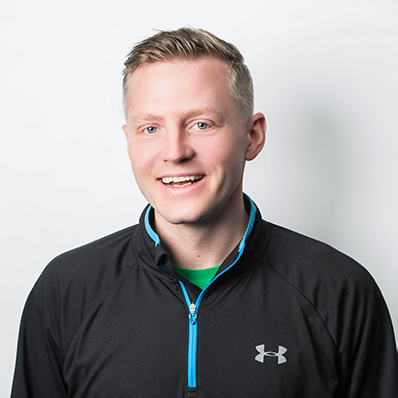
ARTICLE BY:
JOSH REITZ
EMPLOYEE-OWNER, SMART MANUFACTURING BUSINESS CONSULTANT
References:
- https://www.ibm.com/downloads/cas/E3G5JMBP
- https://www.bakerlaw.com/insights/bakerhostetler-launches-2024-data-security-incident-response-report-persistent-threats-new-challenges
- https://www2.deloitte.com/us/en/insights/industry/manufacturing/manufacturing-industry-diversity.html
- https://www.gallup.com/workplace/247391/fixable-problem-costs-businesses-trillion.aspx
- https://www.food-safety.com/articles/2542-recall-the-food-industrys-biggest-threat-to-profitability
- https://commercial.allianz.com/content/dam/onemarketing/commercial/commercial/reports/AGCS-Product-Recall-Report.pdf
- https://www.plex.com/resources/forrester-consulting-study-achieving-412-roi-plex
- https://res.cloudinary.com/wernerelectric/image/upload/v1623704267/commerce/brand/Fiix/Business Impact Study.pdf