Do's and Don'ts of Digital Transformation
- August 20, 2024
- Best Practices
- Automation
Minimize your risks by taking the correct approach to digital transformation
You’re probably excited to start using new manufacturing technologies like AI and robotics (and you should be!), but are you asking the right questions to prepare for your digital transformation? Use this list of do’s and don’ts to avoid common mistakes and take the right approach to digital transformation.
DON'T
RUSH INTO NEW TECHNOLOGY
Implementing new technology can add risks to your business if you don’t take the right approach. Don’t assume investing in new technology will solve all your problems by itself.
DO
BEGIN WITH THE END IN MIND
Start by considering your end goals, and be mindful about how this new technology will help you get there. Before you jump in headfirst, assess your baseline performance, chart your expected improvement and set parameters for how you will determine if the new technology is successful.
DON'T
APPLY IT SECURITY MEASURES TO YOUR OT NETWORK
While an IT network breach can take days to recognize, an operations technology (OT) network outage can cause equipment to malfunction and put workers in harm’s way in seconds. OT technology is often older and not designed to connect to the Internet, which leaves you vulnerable to network outages and production delays. Even smart machines can be vulnerable. Don’t assume your IT protocols will secure your OT network.
DO
PRIORITIZE OT NETWORK SECURITY FROM THE START
The core of any digital transformation is having an OT network that can handle the bandwidth of traffic you will be adding to your network. Is your network sufficient in its current state? Start by performing a security posture survey to receive detailed information that helps you assess and prioritize your OT network security risks. Bring your IT and OT teams together to understand their unique goals and challenges, and work with a partner that can help you protect your assets by designing an IT-OT security organization that addresses the needs of both sides of your network.
DON'T
COLLECT AS MUCH DATA AS POSSIBLE
Often, manufacturers want to upscale the number of data points they are collecting, but not enough people are asking why and what they will do with it. Do you have a plan for using it to make an impact in your business?
DO
START SMALL WITH YOUR DATA
Instead, start with a smaller challenge like a specific work cell. It’s important to understand your company’s policies surrounding artificial intelligence (AI). If it aligns with your company’s AI polcies, run some models with AI and start to understand what anomalies it can find and how it makes an impact on that part of your business. Learn from your mistakes! Once you are confident in how to leverage your data to achieve your desired results, you can scale it to other areas of your operation.
DON'T
FORCE FIT A QUALITY MANAGEMENT SYSTEM
If you are utilizing a quality management system (QMS) that is an offshoot of your Enterprise Resource Planning (ERP) system and not meant for manufacturing, you are missing out on visibility into your quality data. Don’t force fit a solution that doesn’t connect and talk with all the solutions on your plant floor.
DO
USE A DIGITAL QMS DESIGNED FOR MANUFACTURING
It's better to use a digital quality management system that was designed with the manufacturer in mind because it can connect to your other processes and give you a full picture of what is going on with your assets. Digitizing (and automating!) your quality management practices with the right QMS can help you improve consistency and traceability, reduce variation, simplify compliance and more.
DON'T
RELY SOLELY ON VETERAN EMPLOYEES WITH EXPERTISE
Having a group of veteran employees who know your business like the back of their hand is great, but you can’t rely on those employees to be around forever. How will you replace that knowledge gap if they leave?
DO
TRAIN, SUPPORT AND AUGMENT YOUR WORKFORCE
A more long-term solution is to formally document their knowledge, create a succession plan to connect your workforce with the resources they need to learn their job quicker and perform more efficiently. Whether you’re training your workforce, outsourcing technical expertise to support them or augmenting their efforts through technological solutions, investing in your workforce can reduce your skills gaps.
DON'T
ADD EXTRA INVENTORY TO YOUR STOREROOM
If you’re having downtime because parts are failing, it makes sense to invest in a bunch of spare units to have on the shelf, right? It’s not that simple. Don’t spend extra money on parts until you understand why those parts are failing.
DO
DISCOVER THE ROOT CAUSE OF YOUR DOWNTIME
Start by performing an installed base evaluation to catalog where your industrial equipment is located, identify your highest downtime risks and pinpoint obsolete devices. Armed with that information, you can determine what’s causing your downtime, invest in the right amount of inventory and develop a more efficient maintenance system.
DO
WORK WITH A PARTNER THAT UNDERSTANDS YOUR CHALLENGES
Are you ready to start your digital transformation journey? We’re here to support you at every step. Contact your Van Meter account manager or call 1-800-247-1410 to get in contact with a specialist who can help.
BEGIN MY DIGITAL TRANSFORMATION
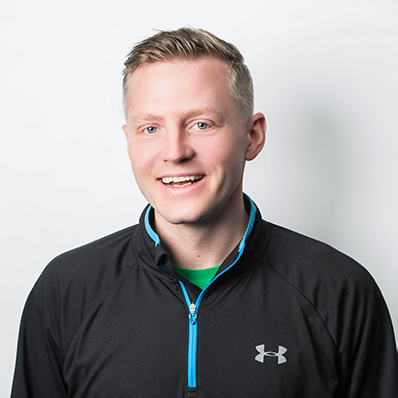
ARTICLE BY:
JOSH REITZ
EMPLOYEE-OWNER, SMART MANUFACTURING BUSINESS CONSULTANT