Five Ways Robotics Can Improve Your Productivity
- December 1, 2022
- Best Practices
- Automation
Whether it is Terminator, I Robot or even Wall-E, robots have often been the subject of futuristic movies and science-fiction—but robots are not just in movies anymore. For OEMs, custom machine builders, system integrators and more, robots are working alongside human workers to improve efficiency and productivity. Do you know how robots could work for you? Read these top five ways robots can improve productivity:
1. Robots consistently work hard.
Without robotics, covering 24 hours of production requires hiring at least three different people for three eight-hour shifts, and each employee will need to take breaks throughout the day. For a one-time investment, one industrial robot can cover all three of those shifts, and can work longer, faster and more flawlessly than human workers. Once they are programmed, robots can perform tasks the same way - every time - without getting tired. Even if some areas of your production require human supervision and input, collaborative robots can safely work alongside humans to do routine, repetitive tasks more efficiently.
2. Robots are safer.
You want to send your workforce safely home to their families each night. Robots do not suffer injuries and can be safely deployed in areas that could be dangerous for their human co-workers. Think of machining processes, like deburring or cutting, where there are physical hazards and caustic chemicals.
In addition, working alongside collaborative robots is safer than working alongside fellow humans because robots can stop performing a function faster than a human. Collaborative robots can sense the slightest bump down to 0.2 Newtons of force and shut down before they harm anybody in their path of motion. For comparison, 0.2 Newtons is about the same force as a slice of bread resting on your palm.
3. Robots are flexible.
There are many different types of industrial and collaborative robots. For example, six-axis industrial robots have six degrees of movement to manipulate products in any direction. You can even swap out the attachment tool at the end of the robot to be able to handle several types of products. Collaborative robots also allow several attachments and can easily be moved to different locations and reprogrammed to perform different tasks when new challenges emerge. Wherever there is a task that requires repetitive action, robots can automate the process.
4. Robots address workforce challenges.
77% of manufacturers say they will have ongoing difficulties in attracting and retaining workers. Supplementing your workforce with robots is a great way to overcome those challenges and improve job satisfaction for your workforce. If you are struggling to find qualified people to perform a task, you can program a robot to perform most tasks. Many workers will not get much satisfaction out of performing mundane, repetitive tasks like placing items in a box. In addition, most employers would rather promote their current employees, and using a robot to do mundane tasks allows your team to engage in other tasks that add more value for your company.
5. Robots reduce downtime and maintenance.
When machines are down, production suffers, but robots allow you to avoid downtime in a couple ways. Robots have fewer spare parts and things that need replaced. They also speed up machine changeover processes. For something like changing over a recipe, you can simply push a button instead of manually changing over an entire machine.
Do you think robots could improve your productivity? Contact your account manager or ask to speak with one of our solutions consultants to schedule a demo and see first-hand how robots can improve all areas of the production process.
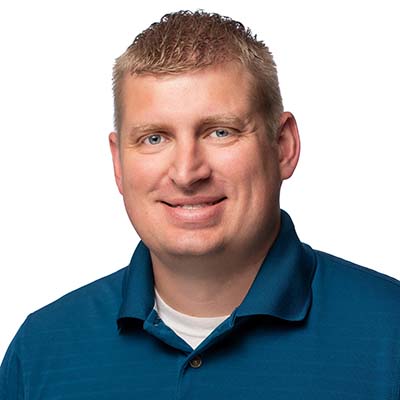
ARTICLE BY:
ZACH DOTSON
SMART MACHINES SOLUTION ARCHITECT