How to create the perfect intelligent motion solution with independent cart technology
- July 11, 2024
- Best Practices
- Automation
Much like peanut butter and jelly, salt and pepper or bacon and eggs, industrial control systems work better when each component seamlessly complements and integrates with the others. You might know how independent cart technology can help you build more flexible, reliable machines, but do you know how easily it fits into your overall Rockwell Automation solution? Whether you’re using iTRAK, MagneMover or QuickStick, read these ways to create a more intelligent motion solution with independent cart technology.
1. TEST AND OPTIMIZE YOUR DESIGNS WITH EMULATE3D™
Independent cart technology isn’t just faster than a traditional conveyor system. When used within Rockwell’s integrated architecture, it’s an intelligent conveyor system that helps you optimize your production. One way to optimize your machine builds is by testing your designs with Emulate3D before you implement them.
Using Rockwell’s Emulate3D™, you can take applications that are in the process of being built and emulate them in software to see what works and what doesn’t. Once you test it in the software, you can make corrections and adjustments before you actually build and deploy. When you’re ready to implement your design, the modularity and flexibility of independent cart technology allows you to fine tune your build for optimal performance.
2. LEVERAGE THE STUDIO 5000® ENVIRONMENT
Software solutions like Emulate3D can test your independent cart technology or robotics systems by binding aspects of the mechanical system to tags in your Logix controller. It even uses the same Studio 5000 environment as the rest of your Rockwell industrial control systems. Skilled labor is hard enough to find without your workforce needing to learn multiple software platforms. With Studio 5000, the people designing and maintaining the system have a common tool they need instead of a separate programming environment for the PLC and separate control systems for the motion and robotics.
3. SAVE TIME WITH APPLICATION CODE LIBRARIES
Since independent cart technology uses the same programming environment as other Rockwell controls, you can utilize Rockwell’s library of pre-tested code to streamline the programming process. Rather than starting from scratch to re-invent the wheel, you can import pre-configured codes into Studio 5000, test them using Emulate3D, then fine tune them to optimize your application.
4. SIMPLIFY YOUR SAFETY SYSTEM
The safety system for iTRAK should also be familiar if you’re using Rockwell’s Kinetix® 5700 servo drives. It uses the same network-based CIP safety as other Rockwell servo drives, so you don’t need hardwired safety. With a minimal learning curve, you can easily monitor your system and set safety parameters over ethernet. Safety comes integrated into iTRAK, so you don’t have to install additional sensors and components after purchase. QuickStick also takes advantage of Kinetix® 5700 servo drives using hardwired STO (Safe Torque Off) and MagneMover has built-in collision avoidance to maintain a safe gap between movers.
5. SYNCHRONIZE SYSTEMS WITH UNIFIED ROBOT CONTROL
Industrial robotics have benefits like improved safety, flexibility and reliability. With Rockwell’s Unified Robot Control, the robot and independent cart system run off Rockwell servo drives and are programmed and controlled through the Studio 5000 environment. Using independent cart technology as part of a unified robot control system, manufacturers can produce more with less space and more flexibly adapt to changing demands.
The single control environment saves time when programming the robot and lessens the skills gap. It also means anyone familiar with Rockwell’s PLCs and software should be able to program and control the robot and machine instead of needing both a PLC and robot programmer.
COMPLETE YOUR INTELLIGENT MOTION SOLUTION
Could independent cart technology fit into your current Rockwell solution? Reach out to one of our smart machine specialists to discuss an application.
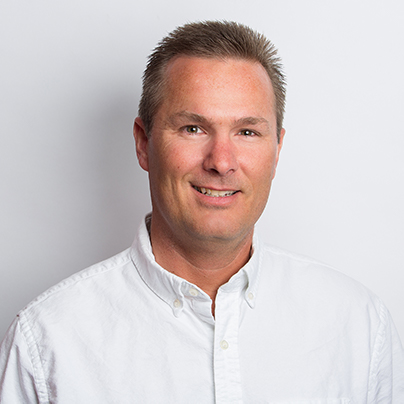
ARTICLE BY:
KIRT HANSEN
EMPLOYEE-OWNER, SMART MACHINES SOLUTION ARCHITECT