Five Risks To Your Business You Might Not Know About
- May 30, 2024
- Best Practices
- Automation
How to identify your business continuity risks
Fear of the unknown comes from lack of predictability and control. Do you know what your risks are for your team and/or organization? How can you predict challenges and control more favorable outcomes? Have you considered these risks to avoid interruptions to your business?
RISK #1: GROWING SKILLS GAPS IN YOUR WORKFORCE
Do you have a lot of veteran employees with years of tribal knowledge in your workforce? That’s great! But what happens to that knowledge when they leave? What if you don’t have a lot of experience to replace them with? Without the right people and processes in place, you risk making mistakes that lead to loss of production.
That’s why it’s important to develop ways to train, support and augment your workforce. Training is the most basic solution, whether you enroll in instructor-led courses or offer e-learning courses to your employees. You can support your workforce by utilizing outside expertise like remote technical support, safety and lockout/tagout services, drive startups, project management and other services. There are also ways to augment, or supplement, your employees through technological solutions like augmented reality and collaborative robots that assist and instruct workers as they perform tasks.
RISK #2: DOWNTIME FROM LEGACY ASSETS AND SUPPLY CHAIN DELAYS
Supply chain delays are still common, so you can’t always rely on expediting parts when your line or machine is down. If one of your critical pieces of equipment goes down, do you have a spare to replace it and avoid the risk of costly downtime? Have you identified your critical equipment? If manufacturing assets or devices are discontinued, where will you find replacements?
The first step in avoiding lifecycle and supply chain risks is documenting your plant floor and storeroom equipment and its lifecycle status with an installed base evaluation (IBE). You will receive a report listing all your equipment, so you can prioritize critical equipment, discover gaps in your inventory, make plans for modernization and reduce your downtime risk. If you want an up-to-date lifecycle status of your equipment, this asset inventory can be maintained in real time in the cloud via the My Equipment app within FactoryTalk Hub.
RISK #3: VULNERABILITY FROM RANSOMWARE ATTACKS
There is a global movement to Ethernet-based networks and devices in the production environment. When you consider the number of IoT connected devices worldwide is expected to grow from 17 billion in 2022 to nearly 42 billion in 2025, it’s no surprise that manufacturing is the most targeted industry for cyberattacks. Production environments and assets tend to go longer without being patched, and many OT networks lack a strong defense-in-depth strategy and toolset.
The average downtime from a ransomware attack is over three weeks, and the average ransomware payment is roughly $400,000. That’s why it’s important to understand what’s on your plant floor, how each asset is connected to other devices and the plant network, where it is in its lifecycle and and what vulnerabilities exist. Once you check those boxes, you can develop a cybersecurity plan that will protect your vulnerabilities as you modernize your system.
RISK #4: DOWNTIME FROM LACK OF PREDICTIVE MAINTENANCE
Do you have a way to fix issues before they cause downtime? If you’re still performing time-based maintenance, you risk unexpected failures from parts with heavy usage and unnecessary labor on parts or machines that have been idle. A reactive or time-based maintenance strategy can lower the lifespan of your machines and result in unnecessary expenses down the road.
How can you predict breakdowns to reduce your risk of downtime and increase the longevity of your machines without a crystal ball? A computerized maintenance management system, like Fiix, can monitor equipment and alert you to potential issues based on real-time and historical data. With more data and insights into your system you can more efficiently schedule maintenance and increase uptime.
RISK #5: BRAND DAMAGE AND LOSS OF PRODUCTION FROM LACK OF QUALITY AND TRACEABILITY
There is an old mindset that quality compliance inhibits production, but it’s actually the opposite if you apply the correct quality practices and solutions. Have you ever considered the risks of failing to address quality? Producing poor quality products can lead to costly scrap, fines, brand damage, recalls, lost capacity and loss of customers.
There are also huge financial risks with poor quality. A product recall means you have to take product back and throw it away plus spend the time and resources to figure out where the incident occurred and replace the defects with no extra profit. You can be fined for failing to comply with government or industry regulations. There’s even the risk of safety and legal fees if your product harms the end user.
Just one quality incident can cost manufacturers millions of dollars in total costs, so it’s worth proactively addressing quality by digitizing your data and implementing ways to track materials through each stage of your production process. When you can use quality data to make faster, more informed decisions, prove regulatory compliance and quickly find the source of your incident, you can address quality issues before they turn into a big financial risk for your business.
ASSESS YOUR RISKS AND VULNERABILITIES
Do you know which of these risks you face? Do you know how to assess your vulnerabilities? Don’t fear the unknown. Help is available! Schedule a free risk evaluation, so we can help better protect your business.
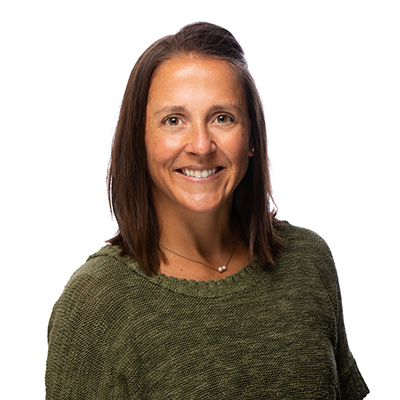
ARTICLE BY:
JACKIE LAFLEUR
EMPLOYEE-OWNER, SMART MANUFACTURING MANAGER
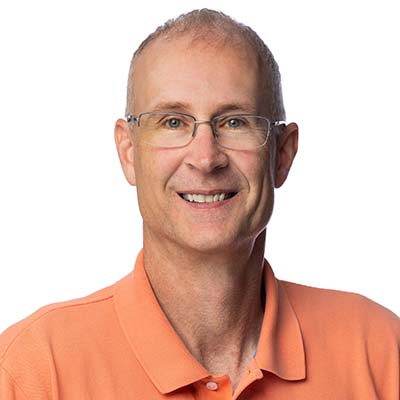
ARTICLE BY:
JEFF HAYES
EMPLOYEE-OWNER, SERVICES SPECIALIST