Five Reasons You Should Invest In Autonomous Mobile Robots
- November 14, 2024
- Best Practices
- Automation
Learn why other manufacturers are using autonomous mobile robots to meet production goals and how you can too
Do you know which technologies manufacturers are investing in right now to gain a competitive edge? Autonomous mobile robots (AMRs) and Automated Guided Vehicles (AGVs) are one of the top investment areas for manufacturers according to Rockwell Automation’s 9th Annual State of Smart Manufacturing Report. Do you know why manufacturers are investing in autonomous mobile robots and whether you could benefit from implementing AMRs? To find out, see if you recognize these signs of when you should consider investing in autonomous mobile robots.
1. YOUR THROUGHPUT DOESN’T MEET YOUR PRODUCTION GOALS
With reduced access to labor and growing operating costs, how do you reach ever-rising production goals with fewer resources? Material handling accounts for 25% of the manufacturing workforce on average. What if you could more quickly and safely move materials through your facility with fewer people? With autonomous mobile robots, you can.
While a leisurely walking pace is roughly 2 mph, an autonomous mobile robot can pick up and carry large payloads across long distances at two meters per second, which equates to 4.5 mph. In addition to being twice as fast, robots don’t get tired or injured and don’t need breaks as often. Some AMRs can work an entire eight-hour shift or longer without charging. If you deploy two or more AMRs for a task, you can continuously have at least one of them running while the other charges.
2. YOU STRUGGLE WITH WORKFORCE RETENTION
Would you enjoy carrying heavy materials across long distances all day? It’s a difficult task that can wear workers down, cause injuries and ultimately lead to a dissatisfied workforce that might be reconsidering their employment options. As manufacturers struggle to find and retain qualified workers, autonomous mobile robots allow them to take workers who are lifting and moving products through the warehouse and re-deploy them to perform tasks that are more meaningful for them and the company. By offering more fulfilling job roles, you’ll be better positioned to retain talented workers.
3. YOU HAVE SKILLS GAPS FROM HIGH TURNOVER RATES
When a worker leaves, how do you quickly replace their knowledge of your plant floor and processes without jeopardizing safety or productivity? High turnover creates costly skills gaps for manufacturers. With autonomous mobile robots, you can pre-map your plant layout and program the optimum routes, so the robot will immediately know how to navigate your plant floor along the most efficient path.
AMRs continue to learn on their own too. As they move through the facility, they can sense obstructions and reroute to the most efficient path from Point A to Point B. Over time, they will even learn how to avoid recurring obstructions. Instead of continuously investing resources into finding and training new workers, a one-time investment in autonomous mobile robots allows you to complete the same material handling tasks in your warehouse with less time and effort.
4. YOU’RE LOOKING FOR WAYS TO REDUCE SAFETY RISKS
High turnover and skills gaps also increase safety risks for your workforce, as new employees are often inexperienced with equipment and take time to learn safety procedures. Even if they do follow safety procedures, having a human behind the wheel of a forklift or interacting with machinery presents the risk of injury.
Autonomous mobile robots lessen the risk of injury by taking some of those humans out of the equation. AMRs are equipped with sensors and in some cases lidar technology, smart cameras or computer vision that can identify both the fixed obstructions that are mapped out in its programming and the variable obstructions like a human walking by or a cart left in an aisle. Instead of leaving safety in the hands of workers who are learning the ropes or tired from a long shift, you’re utilizing technology that has been tested and certified from a safety standpoint.
Plus, repeatedly lifting and carrying heavy items long distances puts unnecessary stress on workers and can lead to injury. Using AMRs to lighten their load keeps your workforce fresh and alert.
5. YOU’RE RUNNING OUT OF FLOOR SPACE
When factory floor space is tight, you don’t always need to invest in more real estate to increase production. Autonomous mobile robots can help you do more with the floor space you already have.
AMRs give design engineers a chance to think outside the box and tap into their creativity when it comes to machine design and line layout. With robots no longer having to be fixed in place, an AMR allows you to condense machine size to save space. If you know your machine will only interface with an AMR, you can design it differently than if a human was going to perform an operation in that work cell. Whether you’re bringing parts to and from the machine or using the AMR to perform a specific operation across multiple machines, using an AMR allows you to be more efficient with your floor space.
SEE AN AUTONOMOUS MOBILE ROBOT IN ACTION
Are you ready to see one of these autonomous mobile robots for yourself? Schedule an AMR demo to see one in person and talk with our robotics experts about possible applications in your facility.
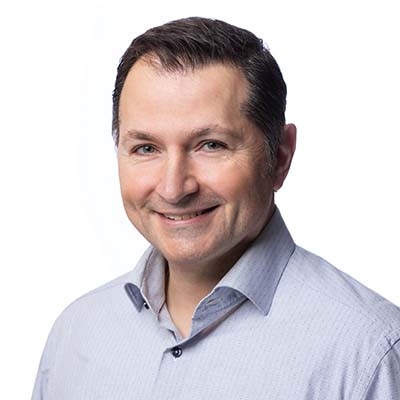
ARTICLE BY:
GEORGE ROVOLIS
EMPLOYEE-OWNER, SMART MACHINES & ROBOTICS MANAGER