Three Tips To Handle The Industrial Workforce Shortage
- January 9, 2025
- Best Practices
- Automation
Use these tips to reach higher production goals with fewer resources
U.S. manufacturing is expected to have 2.1 million unfilled jobs by 2030. Do you have a plan to overcome the industrial workforce shortage? How will you reach increasing goals with fewer resources? Meeting your future goals means having a sound workforce strategy. Be prepared to train, support and augment your workforce with these resources.
TIP #1
TRAIN YOUR PEOPLE
While there is strength in numbers, knowledge is power. Employees who are well-trained in their roles and confident in their skills can get more done in less time. In addition to improving employee retention, 48 percent of organizations see bottom-line growth from training—or reskilling—their employees, and 73 percent see higher employee satisfaction.
Enrolling your workforce in training opportunities, like in-person Rockwell Automation courses, gives your workforce hands-on experience before they use parts and software in a real environment. If an online learning option would work better, Rockwell’s Learning+ platform allows students to learn at their own pace and attend virtual classroom sessions with instructors, labs and Q&A sessions.
TIP #2
SUPPORT YOUR PEOPLE WITH OUTSIDE RESOURCES
Do you know how using outside support for maintenance or technical support can help you increase reliability and avoid costly downtime? Instead of paying someone a salary to be available around the clock, using remote technical support gives you access to experts via phone and chat 24/7/365.
Why pay someone year-round to do a specific task when you can outsource that job only when it is necessary? For example, Van Meter offers on-site support services like drive startups, preventative maintenance, safety audits and more. By using outside resources to help with specialized tasks, you can get more done with fewer resources.
TIP #3
AUGMENT YOUR WORKFORCE WITH TECHNOLOGY
You might think of technology as a replacement for human workers, but do you know how technology can make your workforce more efficient? With high turnover, Augmented Reality (AR) can help employees learn new tasks faster. Instead of asking another employee to instruct them and losing that person’s production, AR overlays digital content—like instructions or drawings—onto the real-world environment. New employees could see instructions and perform tasks simultaneously.
Where do you have people performing monotonous repetitive tasks? Automating those tasks lessens the risk of workplace accidents. If the task is taking a product from a conveyor belt and placing it in a box, have a robot do it instead of a person. The result will be the same—the product will be in the box—but robots will not ask for a salary, they do not have to take breaks and they will not get injured.
DO MORE WITH LESS
Where could your workforce be more efficient? Contact us to book a training, schedule a support service or ask about technology that can help you do more with less.
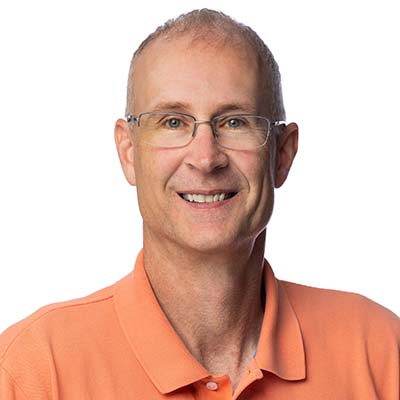
ARTICLE BY:
JEFF HAYES
EMPLOYEE-OWNER, ACCOUNT MANAGER