Busting Myths About Robotic Palletizing Systems
- July 23, 2024
- Best Practices
- Automation
With labor shortages, skills gaps, safety concerns and more, automating your hand palletizing applications can provide meaningful ROI for your business. You’ve probably researched types of robotic palletizing systems, but how do you know which system to invest in? To help you decide, learn how beRobox is busting myths about robotic palletizing.
MYTH #1: IMPLEMENTING A ROBOTIC PALLETIZING SYSTEM IS COMPLICATED
While setting up a robotic palletizer might sound complicated, setting up a beRobox palletizing system requires no prior robotics expertise or programming skills. The beRobox palletizer comes pre-programmed from the factory, so you only need to enter the parameters for box and pallet size to get started. It has an integrated conveyor, so you don’t have to teach the robot how to work with the conveyor or the pallet. Because everything is integrated from the factory, it only takes five minutes to deploy.
MYTH #2: ROBOTIC PALLETIZERS TAKE UP TOO MUCH PLANT FLOOR SPACE
While this myth might be true for a robotic palletizer that uses industrial robots, beRobox uses Doosan collaborative robots (cobots). What’s the difference? Industrial robots require protective guarding that takes up extra space on your plant floor. They also must be anchored down, so you can’t move them around and redeploy them for different tasks.
Collaborative robots don’t require fencing or guarding, and the entire beRobox system can be easily moved around the factory to create more space when needed. You can even move it to a different production line and redeploy it to perform a new task in minutes without calling a robotic programmer to reprogram your system. Plus, the footprint of the beRobox palletizer is smaller than an industrial robot. The result is more flexibility for your floor space and more flexibility in the tasks your robotic palletizer can perform.
MYTH #3: ROBOTS ARE MORE ERROR PRONE THAN HUMANS
If the robot was not properly programmed, this myth could be true, but when programmed properly, robots will make fewer mistakes than their human counterparts. beRobox comes pre-programmed from the factory, so there’s less opportunity for error.
If you enter the correct parameters for box and pallet size during setup, the robot will perform flawlessly unless there is a fault. While a human might take several days or weeks to learn how to do their job well, a robot can follow instructions from day one. With such high turnover in the workforce, using a robotic palletizer can cut down on beginner mistakes and provide more consistent long-term performance.
MYTH #4: WORKING WITH ROBOTS IS DANGEROUS
Is working with robots more dangerous than working with other humans? When palletizing systems use collaborative robots, it is safe for humans to work around them. In fact, Doosan’s collaborative robots carry a PLe, Category 4 safety rating, the highest possible safety rating in the industry and higher than competitive cobots.
Doosan cobots have torque sensing in each of their six joints, so they can sense collisions and shut down to a safe state—often faster than a human can. beRobox’s robotic palletizer also uses safety scanners as an option, so it can slow down or shut down if a human gets too close.
MYTH #5: ROBOTIC PALLETIZERS ARE REPLACING HUMAN JOBS
Given the workforce challenges that manufacturers face, hand palletizing is an area many factories are looking to automate. Does that mean robotic palletizers are replacing human jobs? Not exactly. U.S. manufacturing is expected to have 2.1 million unfilled jobs by 2030, so manufacturers can’t afford to lose the employees they already have.
Instead, they can upskill employees and reassign workers to perform jobs that are more meaningful for the company and more engaging for the employee. Palletizing is hard work, and repeated lifting and twisting can lead to injury. Automating that job allows you to place people in more fulfilling long-term roles and retain quality employees.
MYTH #6: COBOTS AREN’T FAST OR STRONG ENOUGH TO PROVIDE MEANINGFUL ROI
While collaborative robots aren’t as fast as industrial robots, they still palletize faster than humans can. Humans can typically stack one box at a time, but a cobot can provide higher throughput by picking multiple products per cycle.
While automated palletizers that use industrial robots are good for high volume, low-mix applications, a palletizer that use cobots (like beRobox) does better replacing hand palletizing applications that are low-volume and high-mix. beRobox can distinguish between different products of different sizes, so it can handle a mixed in-feed of products and palletize them on separate pallets.
MYTH #7: IT’S DIFFICULT TO TRY ROBOTIC PALLETIZING FOR YOURSELF
Would you like to see how a robotic palletizer like beRobox would work on your plant floor? Trying it for yourself is simple, and we’ll even bring the demo to you. Contact your Van Meter account manager or call 1-800-247-1410 to speak with one of our smart machines and robotics specialists to schedule a personalized demo.
I WANT TO SEE beROBOX IN ACTION
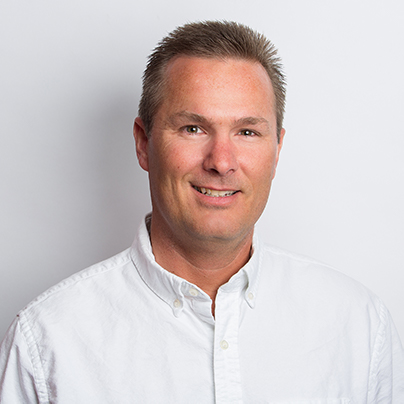
ARTICLE BY:
KIRT HANSEN
EMPLOYEE-OWNER, SMART MACHINES SOLUTION ARCHITECT