Manufacturing Change Management Made Easy: 5 steps for implementing a smart manufacturing solution
- March 26, 2024
- Best Practices
- Automation
If you’ve ever struggled upgrading to a new phone or figuring out where everything is in a new vehicle, you know that change can be challenging. As manufacturers adopt new technologies, automate processes and digitize data, the way their people operate has to change. It doesn’t have to be a struggle though. Use these steps to take advantage of smart manufacturing technology while making change less challenging.
STEP 1: UNDERSTAND YOUR WHY
What makes change so difficult? Even in a situation that is not ideal, familiarity is comfortable. To avoid fear of the unknown, the first step is understanding why you need to change. What are your pain points? What would improvement look like? Your manufacturing goals might include automating compliance documentation, reducing waste, improving safety or solving workforce challenges. It helps to get a strong baseline assessment of people, processes and pain points before jumping to any type of solution and technology.
STEP 2: ENGAGE ALL STAKEHOLDERS
How do you assess those pain points? It’s important to get feedback from diverse stakeholders and identify what is most important to them. What’s important to your employees in one area of the business is probably different from those in other areas.
For example, the financial team might prioritize return on investments, production workers could be concerned with how changes will simplify their reporting processes and plant managers might want quicker access to production KPIs. Once you understand what is important to people, you can develop a solution and show them how it will make their lives easier.
STEP 3: DEVELOP A SMARTER SOLUTION
Manual processes like tracking quality checks, recipes and production run or batch documentation on paper leave room for variation and human error. While pen and paper are simple, there’s also a lack of traceability when something goes wrong. How will you figure out where an error occurred and how you can fix it? With a digital quality management system, a production manager could see what is happening in real time and catch something that goes wrong instead of waiting until the product gets to the end of the run.
After all, change management is about removing the burden, not the operator. Operators are still setting up systems, making sure machines are running properly and responding to alarms to prevent downtime and waste. Smart manufacturing solutions allow them to focus on their skill set instead of manual reporting processes. It might even give them more freedom to diversify their skillset.
STEP 4: IMPLEMENT YOUR SMART MANUFACTURING SOLUTION
Technology without people willing to adopt it does not get you closer to reaching your goals. How do you get your people comfortable with new processes and technologies? Anytime you go from tracking processes on paper to digitizing data, there is a learning curve with the new system, and it can cause inefficiencies as you tweak the system.
During implementation, there should be a shadowing period with system users. Those individuals should be shown how to configure and manage the system until they can maintain it themselves. What does each screen look like? Where do they enter or find production information? Where can they find diagnostics? Showing them how it translates from what they were doing on paper will ensure a smoother transition to digitized processes.
STEP 5: REASSESS THE IMPACT OF YOUR CHANGES
It’s not enough to implement a solution and walk away. Take the time to assess whether you are achieving the goals and improvements you defined in Step 1. What is going well and what is not?
Knowledge gaps are common during change. Are the right stakeholders learning how to leverage the new processes and technology? Are they achieving the intended results? Depending on the technology, additional training might be needed to get workers up to speed. Change management isn’t a one-time process. It’s a cycle of assessing, implementing and reassessing processes and technology until you reach your intended results.
PARTNER WITH VAN METER’S SMART MANUFACTURING EXPERTS
Van Meter’s Rockwell Automation-authorized smart manufacturing team can guide you through any stage of your smart manufacturing journey. Contact us to discuss how you can assess, implement and evaluate solutions to reach your goals.
WORK WITH A SMART MANUFACTURING EXPERT
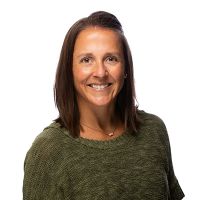
ARTICLE BY:
JACKIE LAFLEUR
EMPLOYEE-OWNER, SMART MANUFACTURING MANAGER