Invest In Them Today and Your Employees Will Stay
- May 31, 2022
- Best Practices
- Automation
When operating a manufacturing plant, how do you decide what is most important to invest in— land, facilities, equipment? Where do you begin? How about with your people? Investing in people and giving your workforce the knowledge, tools and security it needs to perform its best creates a production environment that is conducive to employee retention—a place where people want to come to work, perform at their best and leave at the end of their shift to head home and enjoy their families, passions and hobbies.
Safety First
It is hard enough to find employees—and for a company with a bad reputation regarding safety, it will be even tougher. Keeping your workforce safe starts with identifying what steps you need to take to establish a safety program that includes your production equipment. If you do not have the in-house capabilities to create a safety program, Van Meter can help.
The first step is to perform a Safety Conformity Audit, which gives you a baseline on the status of your machine safety and procedures the audit, we can determine a path forward, implement a plan to remediate safety issues and train employees on safety standards and procedures. In addition to employee retention, increased productivity resulting from fewer lost time injuries contributes to the return on investment for keeping the people you have safe and happy.
Knowledge is Power
Companies with high employee engagement have lower turnover rates, fewer safety incidents, higher productivity and higher profit. Development is one of the key drivers of employee engagement, so it is important to make sure your employees have access to trainings that can develop their skills and make their work more fulfilling.
Van Meter offers both on-site trainings and classes in our facilities on automation and safety. If online classes are more convenient, a platform like Learning+ has virtual training courses that can be self-paced or instructor led. By 2025, 2.7 million baby boomers will retire, and two million jobs are expected to go unfilled, so it is important to invest in your workforce now and make sure it has the knowledge to bridge the impending skills gap.
Industrial Evolution
Attending classes or learning online are not the only ways for your workforce to get up to speed. Technology is a powerful tool to help new employees be productive faster—and have a more enjoyable experience. Through augmented reality (AR), workers can view instructions and perform tasks simultaneously. AR overlays digital content—like instructions or drawings—onto the real-world environment in the same way a SnapChat filter might give you bunny ears.
Industrial technology like robotics and automation eliminates jobs, right? Well—kind of—but that is not the whole story. Automating tasks might eliminate an unsafe job that requires doing monotonous, mundane tasks, but it frees up that worker to do something that adds more value for the company. Most companies would rather elevate current employees to new jobs than lose them, and people will be more willing to stay at a company if their work is more mentally stimulating and fulfilling.
Automation does not have to be the adversary of employment. In most cases, it makes work safe, efficient and engaging. If you have questions about workforce management and how to leverage Van Meter’s solutions to improve employee retention, contact us .
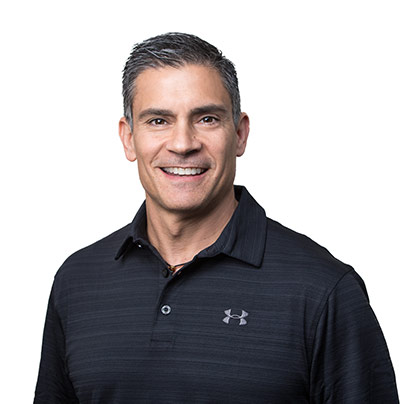
ARTICLE BY:
JEFF SPADARO
EMPLOYEE-OWNER,SALES MANAGER