Eight Ways To Lighten The Load On Your Next Lighting Project
- August 15, 2024
- Best Practices
- Lighting
How to save time and money with lighting services
Lighting projects can get complicated and messy very quickly. With fixtures, drivers, cans and trims (plus the boxes they come in) strewn all over the jobsite, how do you manage and navigate all the clutter to locate and install the parts you need? Good news! You have access to services that can help.1. UNBOX LIGHT FIXTURES AHEAD OF TIME
Unboxing light fixtures on the jobsite is time consuming, and the leftover boxes create workplace clutter. Plus, you are paying electricians a lot of money to do electrical work. Why do you want to pay the same rate for them to do simple work like unboxing materials?
Van Meter can do it ahead of time for a flat fee up front. It might not make sense for a project with a few light fixtures, but when you’re installing hundreds of light fixtures on a large commercial project, saving a few minutes per fixture and removing excess clutter results in labor cost savings.
2. STORE AND TRANSPORT LIGHT FIXTURES WITH LIGHTING CARTS
Once the fixtures are unboxed, how do you get them on the jobsite without damaging them? Instead of loading boxes onto pallets, the opened fixtures can be stored and delivered in lighting carts. Each cart can hold 10 2x4 fixtures or 20 2x2 fixtures.
With heavy-duty caster wheels and adjustable shelving, lighting carts make it easy to transport a variety of fixture types across locations while protecting them from damage. Unlike large pallets, lighting carts can be easily maneuvered through standard doors without needing a forklift for transport. Instead of taking time to unload pallets and dispose of large boxes, the carts are designed for convenient drop off and pick-up and can be replenished for repeated use.
3. KIT AND LABEL LIGHTING MATERIALS
Even with fixtures unboxed and loaded into carts, it can be complicated and time consuming to allocate materials to the correct jobsite location. Make it simple by having materials kitted and labeled together.
Each of your fixtures (and the corresponding hardware) can be labeled with a sticker that has the fixture type, the floor it goes to and the area of the floor where it is being installed. Instead of trying to sort fixture types and count how many should go to each area of the jobsite, you can simply look at the label and take it to the corresponding location.
4. STAGE LIGHTING MATERIALS UNTIL YOU NEED THEM
What do you do with materials until you are ready to use them? Storing materials on the jobsite takes up valuable workspace and puts them at risk of being lost or damaged. On the other hand, waiting to purchase materials until you need them can delay your project with long lead times.
Van Meter offers staging services in its warehouse space, so you can quickly access the materials you need while conserving space on your jobsite. It’s easy to schedule deliveries and manage services through a shared, live document. You can simply update the document when you want certain materials delivered to the jobsite and choose whether you want them to be unboxed and/or labeled ahead of time. With no lead times and no excess clutter, you can focus on keeping your installation on schedule.
5. STAY ORGANIZED WITH LEAN CONSTRUCTION COORDINATORS
Paying electricians to be on a jobsite is expensive. If they’re stuck managing deliveries and organizing materials, you’re not getting the most value out of their time. A lean construction coordinator (LCC) on site can own the organization of your project at a lower cost.
LCCs check fixtures for damage, verify counts are correct, unbox and label materials and more for the duration of your project. The LCC can communicate with Van Meter’s project coordinators to manage deliveries and track where materials are stored, so you can focus on getting more done.
6. PREFAB MATERIALS OFFSITE
Simple tasks like adding fixture whips to light fixtures can be done offsite to conserve space and save labor costs. Van Meter will set up warehouse space with all the whips and connectors laid out, so you can send someone to whip up as many fixtures as you need.
Once the whips are added, you can place them in carts or back in the box and have them delivered to the jobsite. Instead of paying an electrician to add whips onsite, you can send an apprentice to do it offsite for much less cost, and doing it ahead of time reduces installation time once materials make it to the jobsite.
7. MAKE LAMP RECYCLING SIMPLE
Fluorescent and HID lamps must be disposed of properly because they contain hazardous waste. Even LEDs have electronic components that should be recycled. Instead of wasting time and energy trying to manage paperwork and figure out where you can take lamps for disposal, manage your lamp disposal without ever leaving the jobsite.
For a one-time fee, you can purchase a drum or container to put old lamps in. Once it is full, someone will pick up and dispose of the container, and you will receive chain of custody documentation that proves you disposed of the lamps correctly.
8. UTILIZE YOUR LIGHTING EXPERTS
Do you have a partner you can rely on for your lighting needs? Van Meter’s team of lighting specialists and project coordinators can help you solve problems and manage projects more effectively. Call 1-800-247-1410 to utilize any of these services or discover more ways to reduce labor on your next project.
CONTACT WITH A LIGHTING SPECIALIST
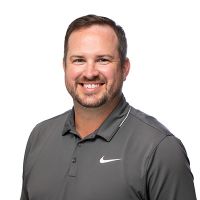
ARTICLE BY:
JOE ROLLINS
EMPLOYEE-OWNER, LIGHTING SPECIALIST